
新聞中心
植物油精煉污水處理工藝改造與生產實踐
2024-12-09
隨著國家對環保的高度重視,近幾年一系列相關政策及標準密集出臺??v觀全國,雖然各地環保要求不同,實施進度也不一樣,但可以看出,行業升級勢在必行;對于企業而言,需不斷提升技術,實現產業升級,同時確保環保達標。目前植物油精煉污水主要成分為油、殘皂、膠質、懸浮物及少量蛋白質等,pH為7~12,屬于高濃度污水。在實際生產過程中,遇車間設備清洗或油品難以加工的情況下,CODCr含量可達(50~60)×103mg/kg,對一般的傳統精煉污水處理工藝負荷沖擊較大,嚴重時可造成生化處理工段填料層嚴重鈣化,細菌無法著床,失去活性,從而導致污水生化處理工段處于癱瘓狀態,造成污水排放不達標,企業面臨環保重大問題\[1-4\]。為了解決以上問題,本文對植物油廠污水處理工藝進行了改造,即在原有工藝上增加預處理工藝,目的是進一步改善污水處理效果和取得更好的經濟效益。
1污水來源及水質分析
1.1污水來源
油脂精煉過程中脫膠、脫酸時水洗離心后產生的工藝污水;化驗取樣口及設備泄漏所產生的污水;真空下水管所產生的水;過濾機吹掃蒸汽冷凝水;冷凍真空系統化冰罐溢流所產生的水;地板清洗水。
1.2采樣、分析方法及評價標準
1.2.1采樣方法
依據《水環境分析方法標準工作手冊》《水和廢水監測方法》第三版進行采樣。
1.2.2評價標準
污水排放標準執行《污水綜合排放標準》Ⅰ級(GB8978—2002)。
1.2.3水質分析方法(見表1)
2污水處理工藝流程
2.1改造前工藝流程
精煉污水首先進入污水收集池,然后進入酸化隔油池,在其進水端加濃硫酸破乳劑,使污水中乳化油轉變為浮油,然后進入一級斜板隔油,去除污水中大部分浮油;再進入反應池,在此投加石灰、混凝劑PAC、助凝劑PAM,然后進入初沉池進行固液分離,使污水中反應生成的難溶性磷酸鹽從污水中分離出來;分離后的上層液進入調節池,與浸出及生活污水在此進行調質,混勻均質后的污水再進入氣浮池分離;之后下層清水進入水解酸化、接觸氧化、二沉池,進行生化反應;為保證污水含磷量穩定達標,最后進入混凝沉淀池進行微細懸浮物的分離,分離液進入清水池達標排放。
2.2改造前存在的問題
在實際生產過程中,精煉污水CODCr含量較高、波動較大時,酸化破乳隔油分離不清,乳化油未得到較徹底分離,雖然加大了濃硫酸用量,但隨后一系列污水處理工藝效果都受到影響,為了調節反應池pH,石灰用量較大,沉淀池沉降效果差,生化段處理難度大,由于石灰用量大,嚴重時水解酸化段填料普遍鈣化,從而使整個生化段處于癱瘓狀態,直接逼停污水正常運行處理。因此,有必要對現有工藝進行改造。
2.3改造后工藝流程
改造后的污水處理工藝流程見圖1。由圖1可知,對原污水處理工藝的改造主要是替代傳統的酸化隔油和一級斜板隔油工藝,新增了預處理工藝,即靜置分離隔油→三級斜板隔油→硫酸亞鐵絮凝后氣浮→芬頓氧化的新工藝。首先精煉污水自流入隔油池,靜置分離隔油,然后進入三級斜板隔油,經隔油處理后,用硫酸亞鐵作為絮凝劑,采用溶氣式氣浮工藝去除水中浮渣,下層清水再進入芬頓氧化裝置,將高分子及生化反應難降解的長鏈有機物氧化分解成小分子物質;然后再進入反應池,在此投加石灰、混凝劑PAC、助凝劑PAM,反應后的污水進入初沉池進行固液分離,使污水中反應產生的難溶性磷酸鹽從污水中分離出來,分離后的上層液進入調節池,與浸出及生活污水在此進行調質,混勻均質后的污水再進入氣浮池分離;之后下層清水進入水解酸化、接觸氧化、二沉池,進行生化反應;最后為保證污水含磷量穩定達標,使之進入混凝沉淀池進行微細懸浮物的分離,分離液進入清水池達標排放。
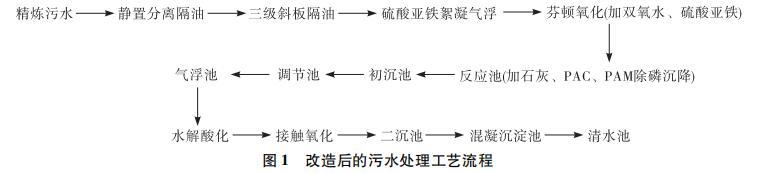
2.4改造后新增的預處理工藝原理及參數
2.4.1靜置分離隔油
沉降池兩座,采用一備一用的進水方式,池內污水沉降時間約24h,水深3~4m,池內安裝集油管,池底設排泥斗,為防止污泥過多沉降,池內安裝雙曲面攪拌裝置,視情況可間歇性攪拌,上層浮油通過集油管排入廢油池。采用靜置分離隔油,池中污水完全處于靜止狀態,自然沉降約24h,可使污水中明油因有足夠長的分離時間而得到有效分離。
2.4.2三級斜板隔油
靜置分離隔油后的污水,再經過144m3三級斜板深度隔油。
2.4.3硫酸亞鐵絮凝后氣浮工藝
三級斜板隔油后精煉污水通過添加硫酸亞鐵絮凝后再氣浮。其中容器氣浮示意圖如圖2所示。
2.4.3.1空壓機
污水量15~20m3/h,空壓機一般選1.5kW或2.2kW。
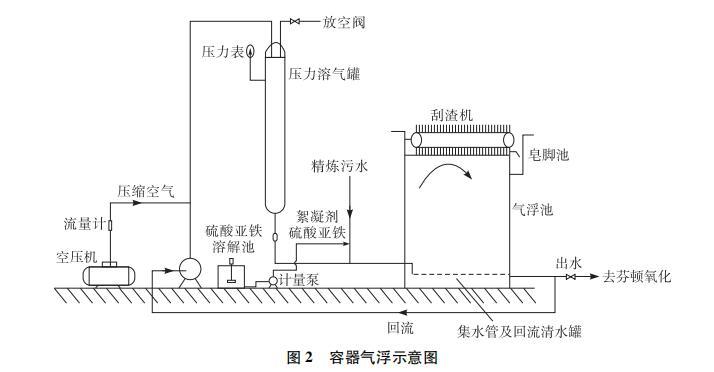
2.4.3.2壓力溶氣罐
密閉的一類受壓容器,是實現水、氣混合并使空氣溶解于水的主要設備,工作壓力0.2~0.4MPa,采用空壓機供氣的噴淋式填料罐,采用無損間接測控,與相應風壓自控配合對溶氣罐中水位、進風量(風壓)完全自動檢測及控制。
2.4.3.3溶氣釋放器
工作壓力0.2~0.4MPa,釋放氣泡的平均直徑20~30μm,釋氣率達99%以上。
2.4.3.4氣浮機
采用全自動氣浮機。
2.4.4芬頓氧化\[5-6\]
芬頓氧化采用的強氧化劑為雙氧水(H2O2)與二價鐵離子的混合溶液,可將很多有機化合物如羧酸、醇、酯類氧化為無機態,氧化效果十分顯著。芬頓試劑中發生的化學反應:Fe2++H2O2→Fe3++OH-+·OH
(1)從式(1)可以看出,1molH2O2與1molFe2+反應后生成1molFe3+,同時伴隨生成1molOH-和1mol·OH?!H具有強氧化能力,其氧化電勢高達2.73V,氧化能力在溶液中僅次于氟氣。因此,持久性有機物,特別是通常的試劑難以氧化的芳香類化合物及一些雜環類化合物,在芬頓試劑中可全部被無選擇氧化降解,從而減輕生化段負荷。芬頓氧化裝置操作簡單,無設備故障。
3生產實際操作
3.1改造后的污水處理工藝中主要構筑物設計參數(見表2)
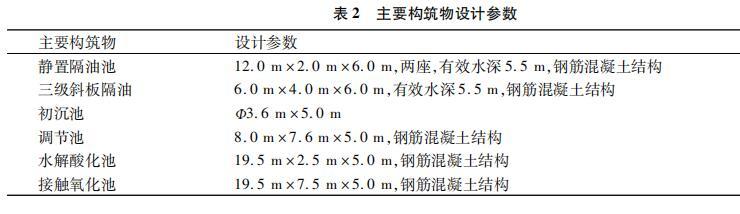
3.2新增工藝操作步驟精煉污水泵入其中一座靜置分離隔油池,到達液位后切換進入另一座靜置分離隔油池,第一座分離池污水在完全靜止狀態下自然沉降約24h,上層浮油通過集油管收入集油斗,下層污水被提升至斜板隔油,依次經過一、二、三級隔油,這樣兩座分離池交替使用,經三級斜板隔油后,精煉污水自流至氣浮池中,同時在自留管線處在線泵入一定流量的硫酸亞鐵水溶液,然后啟動空壓機,調節溶氣罐氣與水進入比,調節好刮渣機,上層浮渣自流入皂腳池,下層清水進入芬頓氧化工藝。溶氣罐氣水比為1∶3;硫酸亞鐵溶液質量分數2%~4%;精煉污水pH7~12;氣浮工藝硫酸亞鐵用量300~500mg/L;芬頓氧化工藝硫酸亞鐵用量0.05%~0.1%,雙氧水用量0.05%~0.1%。
3.3污水處理效果分別對污水處理工藝改造前后的污水中CODCr含量、含磷量、皂腳含量、污泥量及出水水質進行測定,比較改造前后的效果,結果分別見表3~表7。
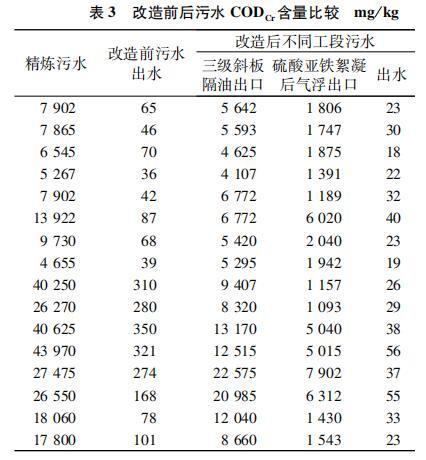
由表3可知,改造前污水出水中的CODCr平均含量為145.94mg/kg,改造后降至31.5mg/kg,平均降低了78.42%。說明新增預處理工藝可有效降低CODCr含量。

由表4可知,改造前污水出水含磷量平均為0.196mg/kg,改造后降至0.042mg/kg,平均降低了78.57%。說明新增預處理工藝可有效降低污水中的含磷量。
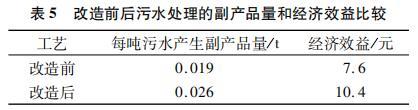
由表5可知,改造前每噸污水產生0.019t的副產品,而改造后,每噸污水產生的副產品增至0.026t,增幅達36.84%。說明新增預處理工藝可使副產品增加。目前副產品的價格是400元/t,可見,效益由原工藝的7.6元增至10.4元,明顯地增加了企業經濟效益。
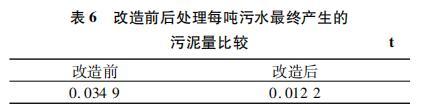
由表6可知,改造前處理每噸污水產生0.0349t的污泥,新增預處理工藝后,污泥量減少至0.0122t,減幅為65.04%。說明新增預處理工藝可有效降低污泥量。
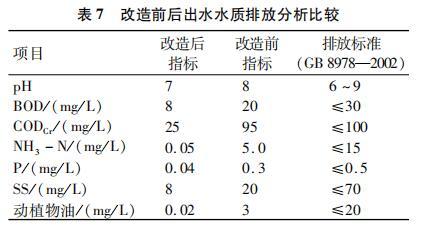
由表7可知,改造前的各項出水指標雖然均能達到排放標準,但改造后各項出水指標不僅達標,且更加環保。說明新增預處理工藝大大提高了污水處理能力。綜上所述,相比原有工藝,新增靜置分離隔油和三級斜板深度隔油,可使污水含油率(動植物油)下降99.33%;通過添加硫酸亞鐵絮凝后再氣浮,CODCr含量平均下降78.42%,污水含磷量平均下降78.57%;在后續原有工藝沉降除磷過程中,石灰用量下降70%~80%,由于石灰用量減少,生化段填料層鈣化率可大幅降低,污水車間污泥量減幅65.04%,水處理成本下降20%~30%;同時氣浮上層浮渣皂腳收集出售,增加了經濟效益,減少了污泥處理費用。
4結論
該套精煉污水處理改造工藝經過一年多的運行實踐,結果表明:新增預處理工藝過程操作簡單,有利于后續生化段水質穩定,對細菌幾乎無沖擊影響,排放出水的水質更環保,100%達到國家一級排放標準,完全適用于植物油脂廠精煉污水的凈化處理。
上一頁:
下一頁:
2024 /
12-09
所屬分類:
解決方案
專業知識
相關資訊—